When most people think of fermentation, they probably think of making beer or wine. But, controlled fermentation can be used for so much more than creating alcoholic beverages.
SRC’s clients bring a variety of products to grow in our bioreactors. For example, we’ve helped develop crop inoculants (agricultural amendments that use beneficial microbes to promote plant health) by growing the microbes in our bioreactors. We’ve also manufactured health therapeutics, animal vaccines, uranium bioleaching preparations and various other products for the agriculture, mining and energy sectors.
How does it work?
In biomanufacturing at SRC, we use fermentation of living organisms to manufacture bioproducts.
Members of SRC’s Biotechnology Laboratories team who do not usually work in the fermentation plant – including me – recently went through a training program to learn how to prepare media for fermentation, use the bioreactors, take sterile samples and disassemble, clean and re-assemble the vessels.
During the training, we used the bioreactors to grow E. coli. Gasp! Isn’t E. coli life-threatening disease-causing bacteria? Well, yes and no.
Some strains of Escherichia coli (E. coli), a bacterium commonly found in the lower intestine of warm-blooded organisms, can cause serious food poisoning. But, most E. coli strains are harmless. In fact, the harmless strains are part of the normal and useful flora of the gut.
E. coli is used routinely in molecular biology as both a tool and a model organism – primarily because it is so easy to work with and inexpensive to grow. In the right environment, E. coli can double in just 18 minutes. Its genetic code isn’t complicated, making it quite versatile. Also, E. coli has been used in labs for decades, so there are a lot of resources available on the subject. Hmm… Seems like the ideal product for fermentation training!
Day 1 – Safety and Preparation
Our group started general lab training with a focus on safety. SRC’s fermentation plant is a BioSafety Level 2 facility, so cleanliness, safety and quality are of utmost importance. To enter the facility, everyone is required to wear a lab coat, shoe covers and safety glasses. We learned how to respond to an emergency biological spill or a bio safety cabinet failure and how to dispose of bio-waste.
Next, we focused on media prep. Two 1-litre flasks and two 30-litre bioreactors were prepared. We used analytical scales to weigh out the appropriate media (a carbon source and a salt). Then, we inoculated the flasks with a small dose of E. coli, which we let grow for about four hours before we transferred it into the 30-litre bioreactors using a pump.
Day 2 – Monitoring
When we entered the facility on the second day of training, our E. coli had grown! E. coli doesn’t take long to reproduce, so after spending the night in the bioreactors, our imminent harvest was looking promising. Most of our second day of training was spent monitoring the bioreactors, taking periodic readings of the vessel’s temperature, stir speed, pH, dissolved oxygen and pressure. We were able to take sterile, contained samples for testing – always steam sterilizing the nozzles between samples to prevent sample contamination.
Day 3 – Final Results
Our E. coli batches were now ready for harvest. So, it was time to take final samples and readings, transfer the batches from the vessels into carboys, shut down and disassemble the bioreactors and start cleaning up. Using a combination of steam, cleaning solutions and an enzymatic cleaner with water, we cleaned the bioreactors and put them back together. Then we disposed of the waste materials through internal utilities to a large regulated waste tank.
Once we were done with the cleaning, we took our samples into the lab to take a look under the microscope. On glass slides, we performed a gram stain (which consists of the addition of various dyes) to the E. coli. Under the microscope, E. coli looks like a smattering of pink rods.
And that’s how to grow E. coli in a nutshell… or, more effectively, in a bioreactor.
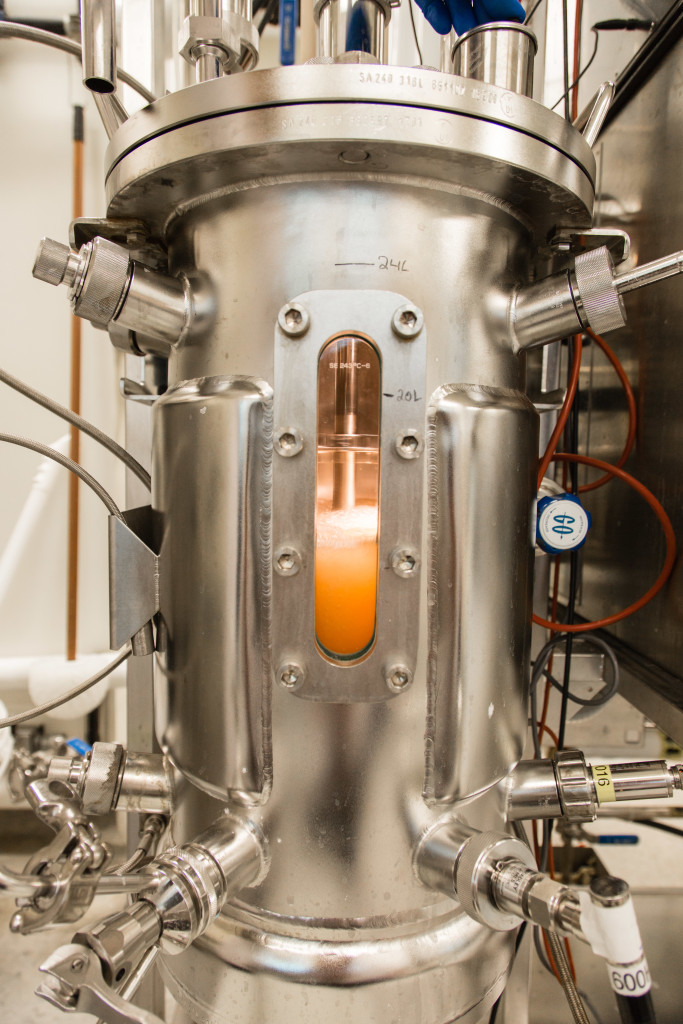
Thirty-litre bioreactor fermenting an E. coli broth.
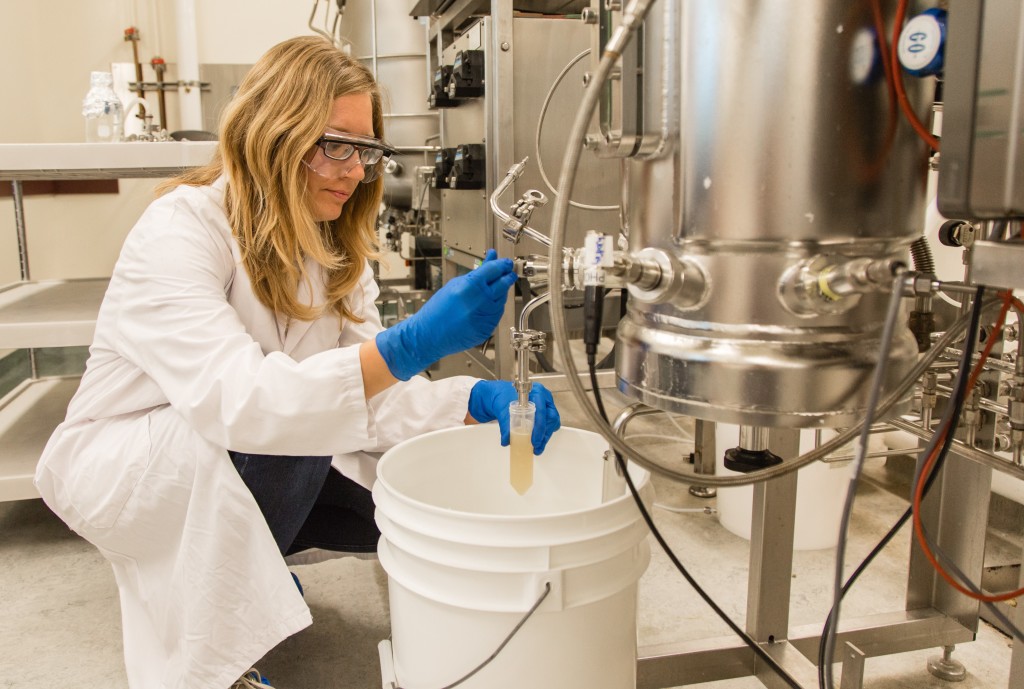
Doré taking a sterile contained sample from the bioreactor.
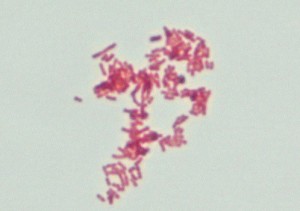
Success! Looking at E. coli under the microscope.
SRC Biotechnology Laboratories is an applied research, biomanufacturing and DNA testing laboratory. Learn more about our lab and our services.
Dore Collett is Business Development Specialist at the Saskatchewan Research Council
This post originally appeared on SRC’s blog about science and technology, From the Lab to the Loading Dock.